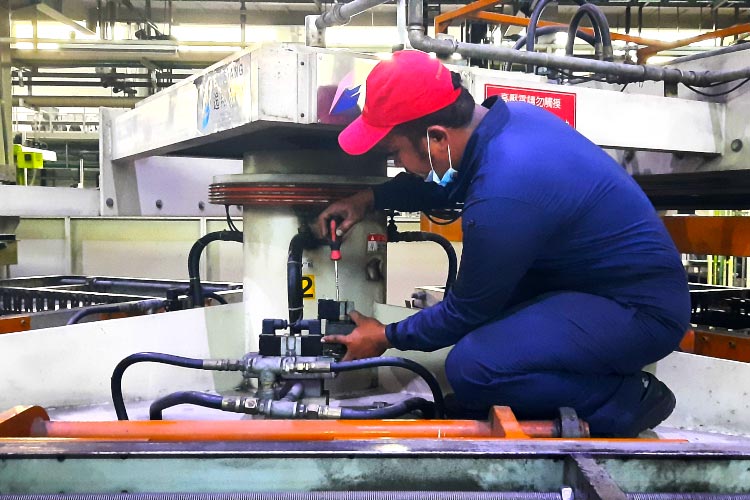
Maintenance
Our facilities personnel always conduct technical maintenance that involves functional inspection, servicing, repair or replacement of devices, equipment, machinery, building infrastructure, and supporting utilities to ensure our manufacturing facilities work as intended.